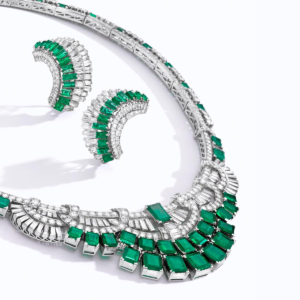
جواهر سازی
هزاران سال است که جواهرات بخشی از فرهنگ بشری بوده و در طول تاریخ برای اهداف مختلفی مورد استفاده قرار گرفته است. در برخی از
رنگ پودری اوایل دهه ۵۰ میلادی توسط دانیل گاستین اختراع شد و در سال ۱۹۴۵ از آن پتنت گرفت .در این فرآیند، مواد پلیمری به صورت پودری با استفاده از شعله بر روی سطوح فلزی پاشیده می شدند. بعد از آن در اوایل دهه ۵۰ میلادی، یک دانشمند آلمانی به نام دکتر اروین گمر یک فرآیند تخته سیال برای رنگ های پودری ترموست ایجاد کرد. در فرآیند معرفی شده توسط دکتر گمر، مواد پودری به صورت الکترواستاتیک بر روی سطوح قطعات پاشیده می شدند و با گرم کردن در کوره، پوششی محکم و مقاوم ایجاد می شدند.
امکان پوشش های ضخیم تر و تخصصی تر: رنگ پودری می تواند بدون ریزش یا چین خوردگی، پوشش های ضخیم تری را نسبت به رنگ های مایع ایجاد کند. همچنین، با رنگ پودری می توان پوشش هایی با رنگ ها، بافت ها، سبک ها و خواص خاصی که با روش های رنگ کاری مایع قابل ساخت نیستند را تولید کرد.
کاهش هدر رفتن مواد: رنگ پودری باعث کاهش هدر رفتن مواد می شود و می توان با استفاده از تفنگ های الکترواستاتیک، رنگ را به صورت یکنواخت و بدون تفاوت بین سطوح افقی و عمودی، بر روی قطعات پاشید. همچنین، می توان چندین رنگ پودری را قبل از گرم کردن آنها، پاشید و افکت های رنگی در یک لایه ایجاد کرد
رنگ های پودری الکترواستاتیک در طیف وسیعی از صنایع و محصولات کاربرد دارند که برخی از آنها عبارتند از:
صنایع فلزی: رنگ های پودری الکترواستاتیک برای پوشش دهی به انواع قطعات و محصولات فلزی مانند پروفیل آلومینیوم، قطعات خودرو، لوله های نفت و گاز، شیرآلات، اتصالات، تابلو های تبلیغاتی، آلات موسیقی و … استفاده می شوند.
صنایع الکترونیک: این رنگ ها برای پوشش دهی به انواع قطعات و محصولات الکترونیکی مانند لوازم خانگی، قطعات الکتریکی، محصولات روشنایی، رادیاتور، بخاری و … مورد استفاده قرار میگیرد . این رنگ ها مزایایی مانند مقاومت در برابر تخلیه الکترواستاتیک، گرما، آتش، انعطاف پذیری، چسبندگی و خواص جدایش کاتدی دارند
صنایع چوبی: رنگ های پودری الکترواستاتیک برای پوشش دهی به انواع قطعات و محصولات چوبی مانند مبلمان، درب و پنجره، قاب عکس، تندیس، تابلو و … کاربرد دارند. این رنگ ها مزایایی مانند مقاومت در برابر خط و خش ، رطوبت، کپک و آفتاب داشته و دارای رنگ های زیبا و بافت های مختلف هستند
خدمات رنگ های پودری الکترواستاتیک در ایران با چالش هایی از جمله عدم آگاهی کافی مصرف کنندگان، عدم حمایت دولت، رقابت با واردات و تحریم ها روبرو است . با این حال از دهه 60 که وارد بازار شد رقابت قابل توجهی با سایر رقبا دارد. و همچنان پتانسیل بالایی برای توسعه و رشد دارد و میتواند سهم بیشتری از بازار رنگ را کسب کند .
مراحل تولید رنگ های پودری الکترواستاتیک به شرح زیر است:
فرمول پیشنهادی :
فرمول تشکیل دهنده یک رنگ پودری الکترواستاتیک پلی استر برای یک تن ممکن است بسته به نوع و کیفیت مواد اولیه، روش تولید، نوع کاربرد و خواص مورد نظر متفاوت باشد. اما به طور کلی می توان گفت که یک رنگ پودری پلی استر حاوی حدود ۵۰ تا ۷۰ درصد رزین پلی استر، ۱۰ تا ۳۰ درصد پیگمنت، ۵ تا ۱۰ درصد هاردنر، ۵ تا ۱۵ درصد فیلر و ۱ تا ۵ درصد مواد افزودنی است.
برای بازاریابی موثر، لازم است که به نکات زیر توجه داشته باشید:
برای تبلیغ رنگ پودری باید مزایای رنگ پودری در مقابل رنگ های مایع و دارای حلال را برجسته کنید. برخی از این مزایا عبارتند از:
• بدون حلال و دوستدار محیط زیست
• امکان بازیافت و کاهش ضایعات
• مقاومت بالا در برابر خوردگی، ضربه، مواد شیمیایی و نور خورشید
• امکان دست یابی به ضخامت بالا و طرح های ظاهری متنوع
• کاهش هزینه های نگهداری و تعمیرات
• افزایش بهره وری و کارایی
• در نهایت باید با مشتریان خود ارتباط داشته باشید و نظرات، پیشنهادات و شکایات آنها را جمع آوری و بررسی کنید. این کار به شما کمک می کند تا نقاط قوت و ضعف خود را شناسایی کنید و کسب و کار خود را بهبود بخشید. همچنین می توانید با ارائه خدمات پس از فروش، مانند گارانتی، آموزش، مشاوره، تعمیر و نگهداری، رضایت و وفاداری مشتریان خود را افزایش دهید.
برنامه بازاریابی فروش موتور محرک تجارت محسوب میشود . و برای ایجاد برنامه بازاریابی نیاز به نوشتن یک بیزینس پلن کاربردی، منسجم و دقیق میباشد
اکسترودر با مشخصات :قطر مارپیچ 25 تا 120میلیمتر متغیر ، سرعت چرخش مارپیچ بین 100 تا 600 دور در دقیقه متغیر، دمای اکسترودر بین 100 تا 200 درجه سانتی گراد متغیر
آسیاب با مشخصات : اندازه ذرات خروجی بین 20 تا 80 میکرومتر ، سرعت چرخش آسیاب بین 1000 تا 6000 دور در دقیقه ؛ تعداد چکش ها یا پین ها بین 10 تا 100 عدد متغیر است و شکل آنها می تواند مستطیل، دایره، مثلث، نیم دایره و … باشد؛ دمای آسیاب بین 40 تا 120 درجه سانتی گراد
کلاسی فایر با مشخصات : عموماً کلاسی فایرهای الکترواستاتیک مورد ترجیح است و مشخصات آنها : اندازه ذرات ورودی بین 100 تا 300 میکرومتر ؛ اندازه ذرات خروجی بین 20 تا 80 میکرومتر ؛ سرعت هوا بین 5 تا 15 متر بر ثانیه
هزاران سال است که جواهرات بخشی از فرهنگ بشری بوده و در طول تاریخ برای اهداف مختلفی مورد استفاده قرار گرفته است. در برخی از
کفپوش رزینی نوعی سیستم کفسازی است که از ترکیب رزینهای اپوکسی یا پلیاورتان و سختکنندهها برای ایجاد سطحی بدون درز، مقاوم و با دوام استفاده
نقاشی کروم یا اسپری نانو اسپری نانو یک تکنیک جدید در صنعت پوشش رنگ آمیزی کروم با اسپری نانو (یا پوشش نانو) میباشد . بر